Elle ***half dir Verhoeven w Isabelle Huppert
Shuen-git rl 周旋捷; Swann Jie sl/, 2011: N°1 Sculptures N°2 好奇藝術::舊+新 Kunstkammer :: Old+New & Film Reviews N°3 Digital Guqin Museum 數碼古琴互動藝術研究創作室 MicroTotalArt HandScroll Guqin; HuaKui cubes; === copyright: when using content of this blog, please use link,indicating source and author information. 版权声明:转载时请以超链接形式标明文章原始出处和作者信息 === http://swannbb.blogspot.fr/2015/02/sgc-2015-monumental-sculptures-etc.html ===
List of Monumental sculpture projects 2015
- 1 http://swannbb.blogspot.fr/2015/02/sunday-robot-play.html
- 2 http://shuengitswannjie.blogspot.fr/2015/02/interactive-reading-room-tea-house-2015.html
- 3 http://swannbb.blogspot.fr/2014/06/neo-ming-bed-luxembourg.html
- 4 http://swannbb.blogspot.fr/2013/02/yuzi-paradise-tell-moon.html
- 5 http://swannbb.blogspot.com/2011/09/12th-changchun-international-sculpture.html
- 6 http://www.saatchionline.com/Shuen-git
Thursday 21 December 2017
Sunday 17 December 2017
bai ji glue receipe by Dominic Eckersley
Dominic Eckersley I'm afraid I neglected to think to take photos from the beginning of the process... but next time I will. That said, I have a lot of the baiji now, enough for a year if it does not go mouldy! I bought two Bletilla Striata orchids easily online for about 6€ each plus shipping. I left them on my terrace and waterered them as normal until the cold set in and their leaves browned and died. I then brought them inside and took one of the plants from the soil. I found a white rhizome and two young green ones growing from it. This was to be expected and these were replanted for next year. I washed the white rhizome in water and scraped the dirt stained skin off, as best I could. I then grated it like I would root ginger with a fine cheese grater. I put it into my pestle and made it into a pulp with the mortar. I remvoed it to a small pan and added about as much water as there was pulp and boiled it for some minutes until the water started to thicken with the extract of the pulp. I added the same amount of water once more and repeated this process until I had a thick porridge. Then I removed it back to the pestle and pounded it once more into as smooth a paste as I could. I then passed it through a tea sieve using a teaspoon to express it through the metal gauze. I collected the gel and bottled it. It took on the consistencey of yougurt more or less. I then put it in the fridge. This extract is also good for medicinal purposes such as reducing inflamation etc. To apply the paste to the string I dipped a finger in the paste and rubbed it much as I had with egg white previously. I cleaned the top board of the instrument from any which ended up on there and allowed it to dry. It did make the 上 a little smoother than before.
Making Baiji glue for silk strings... first I grated the rhizome of the Bletilla Striata orchid with a cheese grater, then mashed it in a pestle and mortar and then boiled it for about ten minutes in water to form a thick paste, and then pressed it through a tea sieve... It dries reasonably quickly and goes on the strings quite nicely. Let's see how it sounds later...
Saturday 16 December 2017
4 star Chinese films! Our time will come 明月几时有; Chinese Van Gogh; Xi Xiang Ji 1927 silent film
Our time will come 明月几时有 ****
Chinese Van Gogh ****
Xi Xiang Ji 1927 silent film ****
Ghost in the Shell 2016 *** half
Chinese Van Gogh ****
Xi Xiang Ji 1927 silent film ****
Ghost in the Shell 2016 *** half
Angry Asian Man: Casting Call: Wong Kar-Wai needs actors for 'Tong ...
Angry Asian Man: Casting Call: Wong Kar-Wai needs actors for 'Tong ...: Famed Hong Kong auteur to direct Chinese American gangster saga for Amazon. It's true. Wong Kar-wai is doing TV. The legendary Hong ...
Tuesday 5 December 2017
Les Joueurs - Marie Monge
30nov, 1, 4, 6 dec
http://cineuropa.org/nw.aspx?t=newsdetail&l=fr&did=342385
http://cineuropa.org/nw.aspx?t=newsdetail&l=fr&did=342385
Marie Monge tourne Joueurs
par Fabien Lemercier
- Tahar Rahim et Stacy Martin en tête d’affiche du premier long de la cinéaste. Une production The Film qui sera vendue par Playtime

La réalisatrice Marie Monge
Depuis le 25 octobre, Marie Monge tourne son premier long métrage : Joueurs. Remarquée avec Marseille La nuit (un film de 40 minutes nominé au César 2014 du meilleur court métrage), la réalisatrice a réuni au casting Tahar Rahim (César 2010 du meilleur acteur pour Un prophète [+], nominé au Lumière 2014 du meilleur acteur pour Grand Central [+], apprécié aussi notamment dans Le passé [+], et à l'affiche récemment dans Le prix du succès [+]), Stacy Martin (révélée dans Nymphomaniac I [+] et II [+], appréciée dans Taj Mahal [+] et Le Redoutable [+], et qui vient de tourner dans Amanda), Bruno Wolkowitch (la série Les hommes de l’ombre), Karim Leklou (meilleur acteur au festival de Turin 2015 pour Coup de chaud [+], à son avantage notamment dans Voir du pays [+], Toril [+] et Si tu voyais son coeur [+]) et Marie Denarnaud (Les Corps impatients, La Taularde [+], Plonger [+]).
(L'article continue plus bas - Inf. publicitaire)
Ecrit par Marie Monge et Julien Guetta avec la collaboration de Romain Compingt, le scénario raconte une histoire d’amour et d’addiction dans l’univers des cercles de jeux parisiens.
Produit par Michaël Gentile pour The Film avec David Pierret comme producteur associé, Joueurs (qui est passé par Les Ateliers d’Angers) a été notamment préacheté par Canal+ et Ciné+ et bénéficie du soutien de l’avance sur recettes du CNC et de la région Ile-de-France. Le tournage se déroulera jusqu’au 20 décembre avec Paul Guilhaume (Ava [+]) à la direction de la photographie. La distribution France sera assurée par Bac Films et les ventes par Playtime.
The Film compte actuellement en post-production Premières vacances de Patrick Cassir (avec au casting Camille Chamoux, Jonathan Cohen, Camille Cottin, Jérémie Elkaïm et Vincent Dedienne Chamoux) et sa filmographie inclut notamment Cherchez la femme [+] de Sou Abadi, Singué Sabour - Pierre de patience [+] d’Atiq Rahimi, Espion(s) [+] de Nicolas Saada ou encore Lolo [+] et Le Skylab [+] de Julie Delpy.
Monday 27 November 2017
Dream of Robot
I dreamt of a white woman, kind of in her 50s, or younger, little bit puffy skinned.
She had put a robot in the oven to bake it - not for eating but for finishing.
I did not see what kind of robot it was, it might not be the geometric robot that I am making
But suddenly the oven door flew open, a whiff of chemical or burnt toxic substance came out of the oven and killed her right there. She was muffled by the toxic substance.
Then I woke up.
This white woman got killed by these robots she made. She had not paid attention to the airing air change condition of the room. She died.
Shocking dream.
I woke up, and thought, was this white woman me?
Or does it have some strange meaning?
I try to find out from the dream book.
---
Today I bought a Borot Avatar from Magnum. A pink robot machine that you wear as an avatar.
But this avatar has a driver seat - you could put your own pilot inside. I bought it through gacha, and received a black cat - black cat pilot. Which i will not use
I use a Sunday Robot as pilot. The thinker Sunday Robot.
Here is a picture of the Borot w Sunday robot.
---
She had put a robot in the oven to bake it - not for eating but for finishing.
I did not see what kind of robot it was, it might not be the geometric robot that I am making
But suddenly the oven door flew open, a whiff of chemical or burnt toxic substance came out of the oven and killed her right there. She was muffled by the toxic substance.
Then I woke up.
This white woman got killed by these robots she made. She had not paid attention to the airing air change condition of the room. She died.
Shocking dream.
I woke up, and thought, was this white woman me?
Or does it have some strange meaning?
I try to find out from the dream book.
---
Today I bought a Borot Avatar from Magnum. A pink robot machine that you wear as an avatar.
But this avatar has a driver seat - you could put your own pilot inside. I bought it through gacha, and received a black cat - black cat pilot. Which i will not use
I use a Sunday Robot as pilot. The thinker Sunday Robot.
Here is a picture of the Borot w Sunday robot.
---
careers-in-3d-printing; Magic Bean mini 3d printer 魔豆3D打印机
https://3dprint.com/193097/careers-in-3d-printing/
Links to live streaming of non stop printing using Magic Bean; wifi printing chip
如果您的打印机不是魔豆打印机,而是常见的开源3D打印机,又想实现像魔豆一样的wifi局域网打印功能,请购买魔豆wifi模块进行改装:
https://item.taobao.com/item.htm?spm=686.1000925.0.0.4a155084rcPNUL&id=557060696148
欢迎在购买前先观看魔豆3D打印机工作视频,魔豆3D打印机直播地址:
https://live.bilibili.com/3806645
如果相对魔豆进行更多了解,欢迎观看我们前5代魔豆3D的研发记录:
http://v.youku.com/v_show/id_XMjc4MzQyMjUxMg==.html?spm=a2hzp.8244740.0.0
It’s not just a fad. Explore how people are using 3D printers in their careers and why it’s important to teach the next generation about this growing technology.
Dr. Alex Chee shows 3D printed surgical models at Maker Faire NY 2017 [Image via MatterHackers]
When speaking with teachers about their efforts to bring 3D design and 3D printing programs into their K-12 classrooms, the one pervasive question is still – why? Teachers try to get funding from administration and are asked – why do you need a 3D printer? Administration springs funding on teachers earmarked for 3D printers, and teachers ask – why do I need to take time out of my classroom to teach how to use a 3D printer? Teachers introduce 3D printing to their classrooms and the parents ask – why are you wasting my child’s time with some “fad”?
Answer – preparation for future jobs. And current jobs. ALL the jobs. Medicine, video games, architecture, manufacturing, product design, special effects for TV and movies, automotive, entrepreneurial efforts we’ve never even heard of (like desktop 3D printers themselves were in 2011) and more all require some form of 3D modeling skills. And the tool of choice to fabricate those models in reality – prototype or final product – is 3D printing.
Teaching simple 3D modeling software like Tinkercad in schools not only prepares students to broaden the scope of job opportunities they might not have considered before, but the practice of designing something in CAD software also covers core STEAM (science, technology, engineering, arts, and math) standards that need to be taught anyway.
Engagement is the unique factor here. Teachers need to work especially hard with the current generation to grab their attention and keep them engaged. Brains are changing. There are more tactile learners and kids that have various issues with paying attention than ever before (even if that issue is being distracted by the cell phone in their pocket.) Incorporating 3D design and 3D printing into the lessons teachers need to teach anyway makes the lesson stick and the classroom time more fun.
Read the full article, including examples of vocations you may not have thought about before which require 3D modeling and 3D printing skills — medicine, architecture, manufacturing, product design, special effects for TV and movies, anthropology, automotive, entrepreneurial — at MatterHackers.
Discuss education, careers, and other 3D printing topics at 3DPrintBoard.com or share your thoughts in the Facebook comments below.
===
smallest sturdy 3d printer, ultimaker style
http://v.youku.com/v_show/id_XMjc4MzQyMjUxMg==.html?spm=a2hzp.8244740.0.0
Magic Bean mini 3d printer 魔豆3D打印机
http://v.youku.com/v_show/id_XMjc4MzQyMjUxMg==.html?spm=a2hzp.8244740.0.0
Magic Bean mini 3d printer 魔豆3D打印机
now, 2299rmb on Nov25 2017
欢迎在购买前先观看魔豆3D打印机工作视频,魔豆3D打印机直播地址:
如果相对魔豆进行更多了解,欢迎观看我们前5代魔豆3D的研发记录:
如果您的打印机不是魔豆打印机,而是常见的开源3D打印机,又想实现像魔豆一样的wifi局域网打印功能,请购买魔豆wifi模块进行改装:
https://item.taobao.com/item.htm?spm=686.1000925.0.0.4a155084rcPNUL&id=557060696148
欢迎在购买前先观看魔豆3D打印机工作视频,魔豆3D打印机直播地址:
https://live.bilibili.com/3806645
如果相对魔豆进行更多了解,欢迎观看我们前5代魔豆3D的研发记录:
http://v.youku.com/v_show/id_XMjc4MzQyMjUxMg==.html?spm=a2hzp.8244740.0.0
Wednesday 22 November 2017
carbon fiber guqin generation #2 WHO, strings
Some choices of metal strings for my carbon fiber guqin #2 "WHO" qin
https://item.taobao.com/item.htm?spm=a21wu.10013406.0.0.16ffd769PIwDZw&id=523018580988&toSite=main
https://item.taobao.com/item.htm?spm=a21wu.10013406.0.0.16ffd769PIwDZw&id=523018580988&toSite=main
Sunday 19 November 2017
Sunday 12 November 2017
ROBOTIC ARM 3d printing DIRK VAN DER KOOIJ
ROBOTIC ARM 3d printing DIRK VAN DER KOOIJ
http://www.3dprinterworld.com/article/dirk-van-der-kooij-3d-prints-endless-chair-with-robotic-arm-and-recycled-refrigerators
http://www.3dprinterworld.com/article/dirk-van-der-kooij-3d-prints-endless-chair-with-robotic-arm-and-recycled-refrigerators
Tuesday 7 November 2017
new-eu-standard-ppe-forestry-high-visibility-orange-bright-pink
http://blog.stihl.com/practical-knowledge/2016/04/new-eu-standard-ppe-forestry-high-visibility-orange-bright-pink/
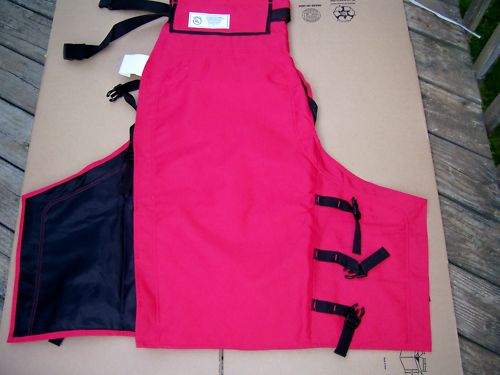
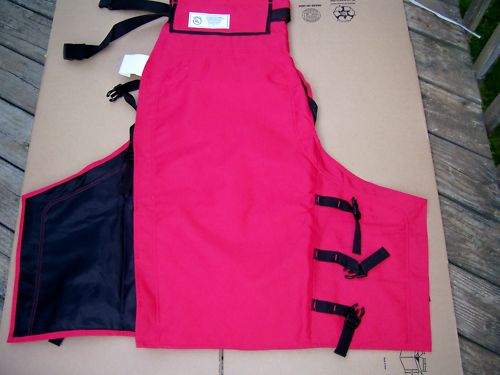
New EU standard for PPE Forestry: from high visibility orange to bright pink
The personal protective equipment for the forestry industry, aka PPE Forestry, is now becoming even safer. Drawing on the results of a major study, a new standard governing work clothing will come into force on 1 May 2016; high visibility orange will be changing to bright pink. Millions of foresters and forestry workers are now facing a race against time to equip themselves for the new standard.
Study: pink is the most effective high visibility colour
Over the years, the effectiveness of high visibility orange, the colour used until now, has been questioned time and again by industry experts. Professionals from northern Europe have complained that clothing with segments of high visibility orange, sometimes also in combination with green, is not sufficiently conspicuous in autumnal forests. For this reason the EU Commission for Forestry and Forest Work has spent the last three years conducting a major study throughout the European Union. As part of the study, both cognition tests and adrenaline measurements were performed on over 10,000 professional forestry workers.
The neuropsychologists behind the tests discovered that the conspicuousness of the high visibility colour used to date truly is unsatisfactory in the forest. “The most important thing about a high visibility colour is the contrast,” explained the commission’s chair Mr. Jack Lumber. “Especially in northern Europe, where the leaves turn orange in autumn, the colour tone currently used is just not effective enough.” To find a solution to this problem, a number of alternative high visibility colours were trialled with test subjects. The key aspect for the researchers was how easily the colour could be seen, even over larger distances. Only one colour caused adrenaline levels to rise significantly in the test subjects, indicating a strong sense of awareness. The assessments of the subjects themselves backed up these findings and led to the only possible conclusion: bright pink is the most easily seen and elicits the required level of caution.
Bright pink is to become mandatory from May 2016
The finding of the study has now been codified for industry application in a new EU standard. To improve safety in the forest immediately, forestry workers must wear protective clothing with segments in bright pink (RGB 255,3,206) from May 2016. From this date high visibility orange will no longer be permitted. Furthermore, the impact will be accentuated through the use of neon or fluorescent dyes.
3d printer using E waste, Gnikou
Saturday 4 November 2017
#1 Contemporary Chinese Design
Hulu shaped electric universal adapter
Hulu is a mystical container a taoist vehicle - magic shape, where an entire world could be contained.
Its a poetic shape especially for electricity.
How did a designer convince the manufacturer to make this fantasy shape?
I have never seen one before, this one I found at a remote farmers market.
This is the China that I like to visit. Something somewhere someone enabled an idea to come to reality. And it is so humble and small, but its done.
The colors are quite local too. Beige color and pale peacock blue. and the font used, the designer definited just did it to his liking. The combination is not your normal "designer" look, nor the execution, we could see little unsmooth surface. The letters used is almost like a careful hand writing and not our industrial high precision "arty" fonts.
Altogether it has a slight "simple innocent" look. Adorable.
Somebody got an idea, and it was granted at the factory and its been made.
I wonder if its a common design, you could buy easily?
Hulu is a mystical container a taoist vehicle - magic shape, where an entire world could be contained.
Its a poetic shape especially for electricity.
How did a designer convince the manufacturer to make this fantasy shape?
I have never seen one before, this one I found at a remote farmers market.
This is the China that I like to visit. Something somewhere someone enabled an idea to come to reality. And it is so humble and small, but its done.
The colors are quite local too. Beige color and pale peacock blue. and the font used, the designer definited just did it to his liking. The combination is not your normal "designer" look, nor the execution, we could see little unsmooth surface. The letters used is almost like a careful hand writing and not our industrial high precision "arty" fonts.
Altogether it has a slight "simple innocent" look. Adorable.
Somebody got an idea, and it was granted at the factory and its been made.
I wonder if its a common design, you could buy easily?
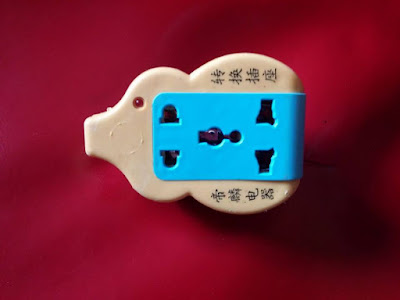
Thursday 2 November 2017
Primitive Log Cabin Build (in Forest) step by step, beautiful wood work
http://www.theshelterblog.com/primitive-log-cabin-build-forest/
Primitive Log Cabin Build in Forest
Very interesting from A to z, how to build a log cabin from clearing, transporting logs from one spot to the clearing (using belts), cutting down trees, with an axe! Just a few hits and the tree comes down. Very informative. Beautiful log cabin.
Published on Sep 15, 2017
Subscribe to:
Posts (Atom)