https://swannbb.blogspot.com/2024/03/molihua-generated-by-ai-using-lyrics.html Discovered an ai app online, free... you could have AI generate a song for you, you must write your own lyrics, and specify which style you would like. So, I wrote a version of Molihua - Jasmine - and asked it to do it in James Brown soul style, then Dimash kazaks folk ballade style. I had wanted to do also Janis Joplin rock, but the software kind of froze. So here are the results. What do you think? so I wrote a simple lyric and put it to molihua james brown, also molihua Dimash... have a listen... :) create your own song with AI. I input my own lyrics, and asked for a James Brown soul version. Stay tune, and see what AI produces...
Shuengit / Swann Jie : MicroTotal Art, Monumental Sculpture, virtual world, film+book reviews
Shuen-git rl 周旋捷; Swann Jie sl/, 2011: N°1 Sculptures N°2 好奇藝術::舊+新 Kunstkammer :: Old+New & Film Reviews N°3 Digital Guqin Museum 數碼古琴互動藝術研究創作室 MicroTotalArt HandScroll Guqin; HuaKui cubes; === copyright: when using content of this blog, please use link,indicating source and author information. 版权声明:转载时请以超链接形式标明文章原始出处和作者信息 === http://swannbb.blogspot.fr/2015/02/sgc-2015-monumental-sculptures-etc.html ===
List of Monumental sculpture projects 2015
- 1 http://swannbb.blogspot.fr/2015/02/sunday-robot-play.html
- 2 http://shuengitswannjie.blogspot.fr/2015/02/interactive-reading-room-tea-house-2015.html
- 3 http://swannbb.blogspot.fr/2014/06/neo-ming-bed-luxembourg.html
- 4 http://swannbb.blogspot.fr/2013/02/yuzi-paradise-tell-moon.html
- 5 http://swannbb.blogspot.com/2011/09/12th-changchun-international-sculpture.html
- 6 http://www.saatchionline.com/Shuen-git
Sunday 31 March 2024
Molihua generated by AI using lyrics that i just put together
Sunday 10 March 2024
Michelle Wong MJ: 17yr old sang Dimash new song, how to do your own karaoke track for singing covers
A very kind young singer 17yrs old from Malaysia @MichelleWongMJ told me how she isolated tracks for singing her own vocals. She sang the new Dimash song as gift to Dimash.
2 hours ago (edited)@MichelleWongMJ
Saturday 9 March 2024
Wednesday 6 March 2024
10-best-music-transcription-software/
https://latouchemusicale.com/en/10-best-music-transcription-software/
Would you like to discover the best music transcription software? You’ve come to the right place!
Finding sheet music for certain songs or arrangements on the Internet can be tedious. And it’s even more complex to transcribe them yourself.
Fortunately, as technology continues to advance, a number of software programs and applications have emerged that specialize in transcribing musical notes. These tools enable us, in just a few minutes, to obtain a transcription of a given song that would have taken us hours or even days to transcribe ourselves.
In this article, we present the 10 best applications for recognizing and transcribing songs into musical notes. They’ll all come in handy and save you a lot of time.
Tuesday 27 February 2024
DIY singing experiment log book : The Listening of a new song, Dimash Qudaibergen - "When I've got you"
Dimash Qudaibergen - "When I've got you" OFFICIAL MV
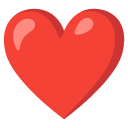


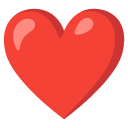
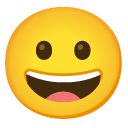
The 10 Best Free Music Transcription Software and Apps
Show less 2Reply
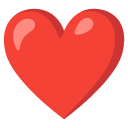
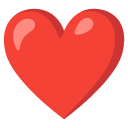
A polish fan tells me:
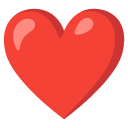
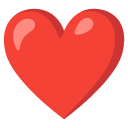
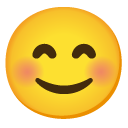
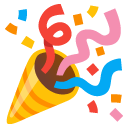
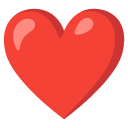
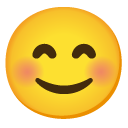
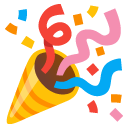
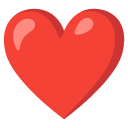
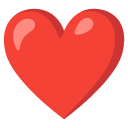
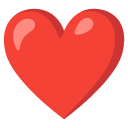
The image adds something dramatic, gothic to the sweet, honey sweet image of the standard D as has been cultured all along. This is his new safe, dark style, a little drift, to add variety to the existing bland sweet standard - w a pretty lady behind. Woman looks feminine knows her sex appeal and power already. She could act out her wishes if she likes. The I got you I, must be D, because we dont know who she is. We are here because of D, so the I is D. Those long claws, mainly attractive to cos play, younger adolescents or for adults niche adult bdsm game players.